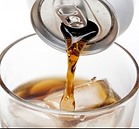
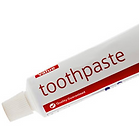

Unilever is a strong competitor of P&G and the company has been striving to improve productivity using the Total Productive Program(TPM). With a market cap of $ 816 B, Unilever’s products are distributed through distribution centers, group-operated facilities, satellite warehouses, public storage depots, wholesalers, independent grocery stores, co-operatives, and various food service providers. A simple philosophy of TPM – if small defects are controlled, large breakdowns can be avoided. As a part of TPM program, Unilever found that 90% of the problems on packaging lines were due to incorrect maintenance & operating standards which were immediately fixed.
As one of the largest CPG companies, P&G has implemented several benchmark strategies. In the manufacturing arena, they are considered one of the best in the world. Their IWS (Integrated Work Systems) principles (similar to Six Sigma, Lean) help set the foundation for a world class organization. IWS is a cost-saving approach which focuses on productivity. This program has resulted in 50% less planned downtime in the manufacturing units. The total impact of these cost-saving measures is expected to generate savings of around $1.2 billion in 2013.
Nestle is a global player with 29 of the brands with annual sales of over $ 1B. Nestle implemented the 5 guiding principles of Lean thinking:
- Engage our people
- Understand value
- Evaluate which values add value & which do not
- Eliminate non-value added activities
- Continuously improve value creation
The Nestle Continuous Excellence(NCE) program was implemented to eliminate confusion while helping improvements. The management system consolidates principles of Lean manufacturing, TPM, Six Sigma, 5S and other quality and productivity principles to eliminate confusion, redundancy and waste and to improve quality.
Coca-Cola Company implemented Six Sigma under the heading of Business Process Excellence (BPE), a complete program to help run the business. This differs from the approach many companies are taking, where these firms are narrowly implementing Six Sigma today in manufacturing, and do not see it as a way to run and manage the entire business – merely a tool to improve a process or an operation. Coca-Cola looks at it much more as a way to connect the business parts with one another – that is an important element.
Researchers in Coca Cola have applied the Six Sigma approach to reducing water consumption, minimize waste, and water losses for the cola industry. The excellent results obtained with the project for reducing water use led Coca Cola to apply Six Sigma to other projects such as the reducing power consumption, reducing raw material waste, and improving their products.
Key Players
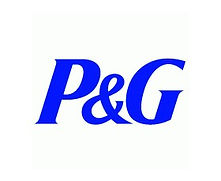



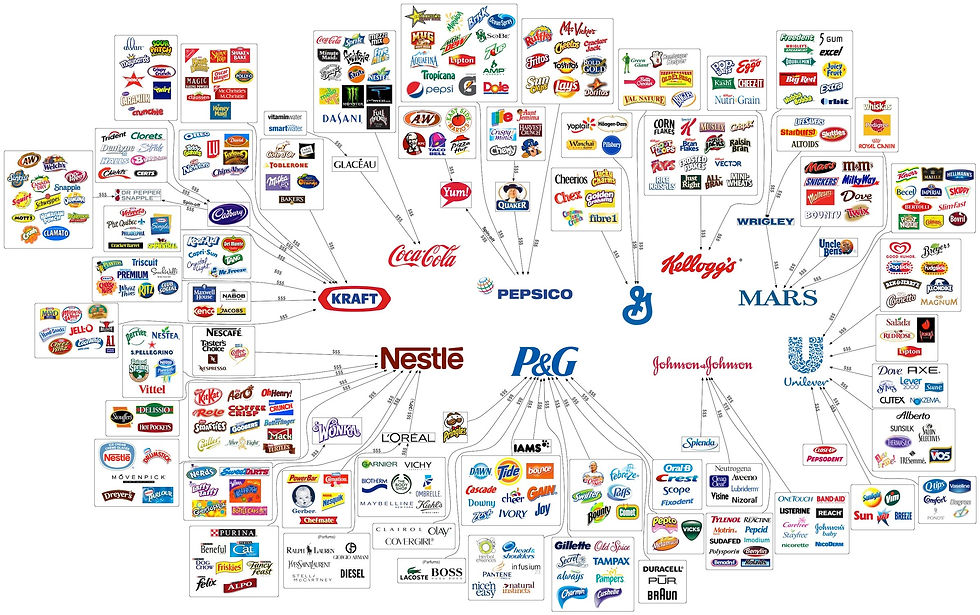

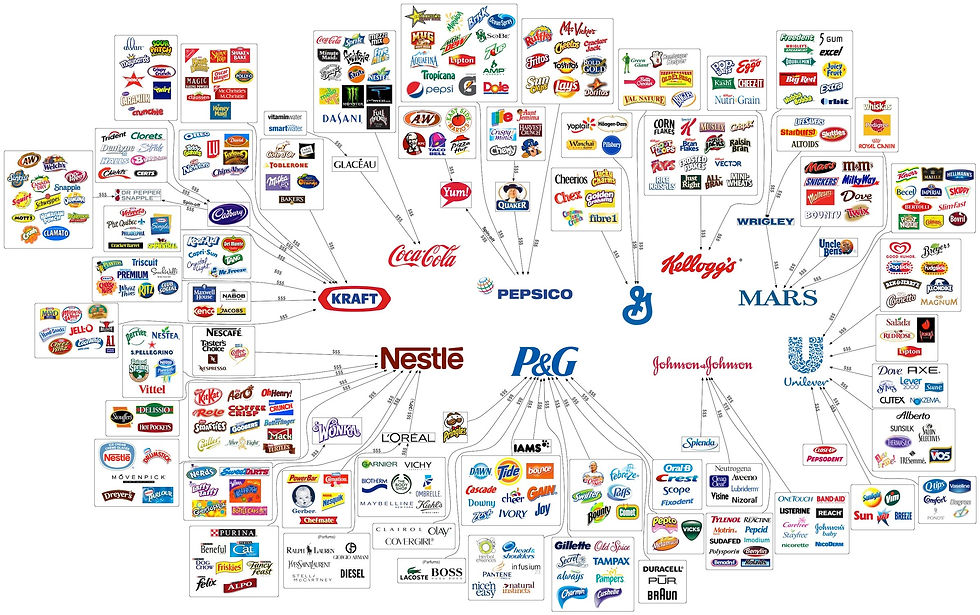
